Zhengzhou Rongsheng Kiln Refractory Co., Ltd. focuses on the research and development, production and sales of refractory materials. Refractory bricks mainly include magnesia bricks, corundum bricks, spinel bricks, AZS bricks, wear-resistant high-alumina bricks, anchor bricks, mullite bricks, etc. Products are widely used in many fields such as electricity, metallurgy, nonferrous metals, petrochemicals, building materials, etc.
The following are some of Rongsheng’s hot-selling refractory bricks. Welcome to contact us for more products and cheap price: info@refractorymanufacture.com
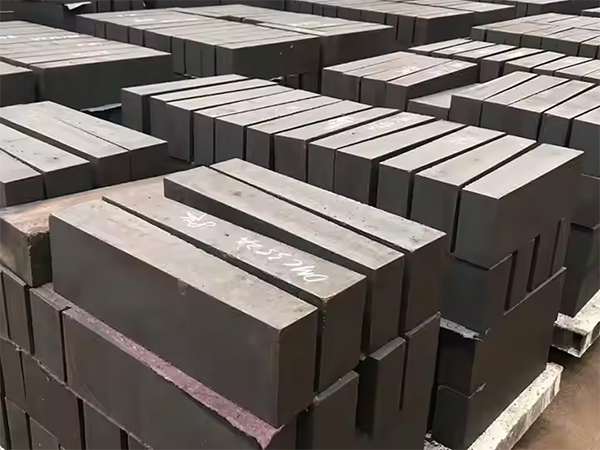
Magnesia Refractory Bricks
Type: Fused Magnesia Brick, Magnesia Chrome Brick, Magnesia Carbon Brick, Magnesia Iron Spinel Brick, Magnesia Alumina Spinel Brick, Magnesia Zirconia Brick;
Refractoriness: ≥1500°C
Main Component: MgO
Application: Widely used in metallurgy, cement, ceramics, glass and etc industries
Note: Any Interests for our magnesia bricks, emial us for quotation & more information:info@refractorymanufacture.com

Mullite Refractory Bricks
Type: Mullite Brick, Corundum Mullite Brick, Zircon Mullite Brick;
Refractoriness: ≥1600°C
Main Component: Al2O3
Application:Widely used in metallurgy, glass, chemical industry, electric power and etc industries
Note: Any Interests for our mullite bricks, emial us for quotation & more information:info@refractorymanufacture.com
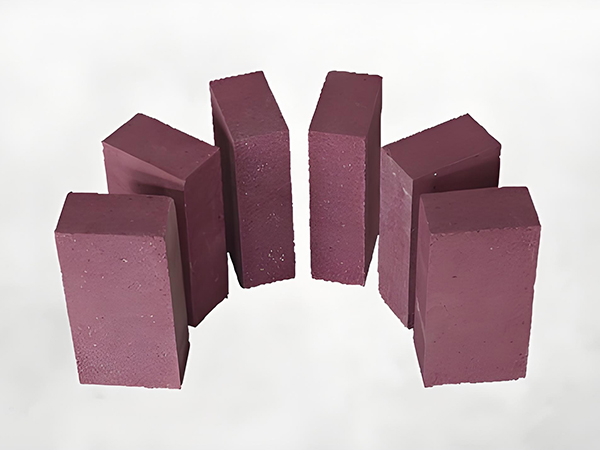
Corundum Refractory Bricks
Type: Fused Corundum Brick, Chrome Corundum Brick, Mullite Corundum Brick;
Refractoriness: ≥1700°C
Main Component: Al2O3
Application: Widely used in metallurgy, ceramics, glass, chemical industry and etc industries
Note: Any Interests for our Corundum bricks, emial us for quotation & more information:info@refractorymanufacture.com
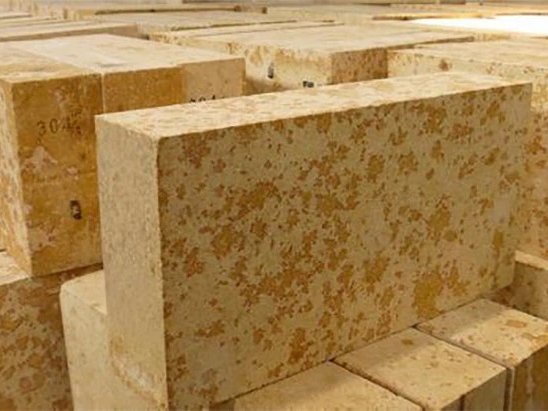
Silica Refractory Bricks
Type: Silica Brick, Sillimanite Brick, Alumina Silica Brick;
Refractoriness: ≥1500°C
Main Component: SiO2
Application:Mainly used for building coke ovens, also suitable for kilns in glass, ceramics and etc industries
Note: Any Interests for our silica bricks, emial us for quotation & more information:info@refractorymanufacture.com
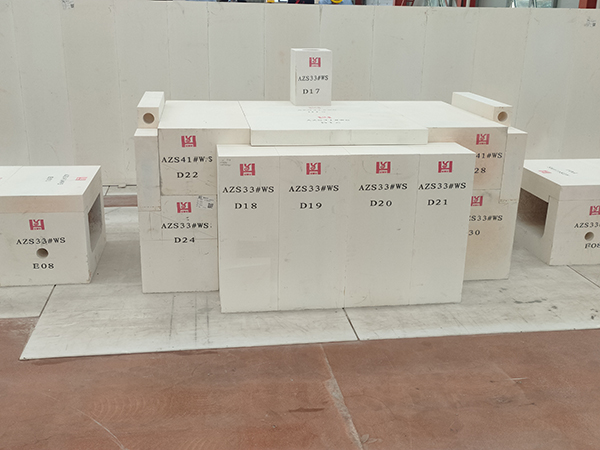
Fused Cast AZS Refractory Bricks
Type: Fused Cast AZS#33, Fused Cast AZS#36 and Fused Cast AZS#41
Refractoriness: ≥1800°C
Main Component:ZrO₂+Al2O3
Application:Widely used in steel-making furnace、glass kiln and other high temperature furnaces
Note: Any Interests for our azs brick, emial us for quotation & more information:info@refractorymanufacture.com
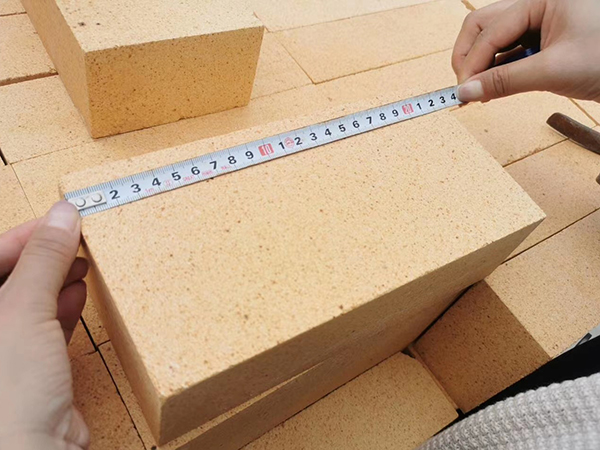
Alumina Refractory Bricks
Type: High Alumina Brick, Alumina Carbon Brick, High Alumina Refractory Ball, Alumina Bubble Brick, High Alumina Shaped Bricks;
Property: High refractoriness, Good thermal shock resistance,Strong acid erosion resistance, Great wear resistance, Low thermal expansion coefficient & High thermal conductivity
Application: Basic open-hearth furnace for steel making, Electric furnace bottom and wall, Permanent lining of oxygen converter,Non-ferrous metal metallurgy furnace
Note: Any Interests for our alumina bricks, emial us for quotation & more information:info@refractorymanufacture.com
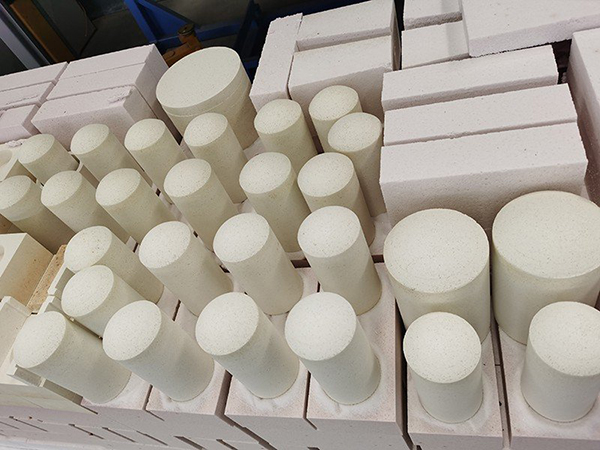
Zircon Refractory Bricks
Type: Zircon Brick, Zirconia Corundum Brick, Zircon Mullite Brick;
Refractoriness: ≥1500°C
Main Component:ZrO₂+Al2O3+SiO2
Application:Widely used in high temperature kilns in metallurgy, ceramics, chemical industry and etc industries
Note: Any Interests for our zircon bricks, emial us for quotation & more information:info@refractorymanufacture.com
The following are applicational cases of refractory bricks in modern industry
Metallurgical industry
1. Steel smelting
Blast furnace system: corundum mullite bricks (Al₂O₃≥75%) are used in the throat, and silicon carbide bricks (SiC≥85%) are used in the belly;
Converter lining: magnesia carbon bricks (MgO≥76%, C≥14%) can resist 1700℃ molten steel scouring;
Electric furnace roof: prefabricated corundum castables are used to achieve overall molding, and the anti-stripping performance is improved by 40%;
2. Non-ferrous metal smelting
Copper flash smelting furnace: chrome corundum bricks (Cr₂O₃ 15%-30%) to resist FeO-SiO₂ slag corrosion;
Aluminum electrolytic cell: Silicon nitride combined with silicon carbide lining (Si3N4 combined with SiC) to achieve a service life of 1300 days;
Building materials industry
1. Cement Kiln
Rotary kiln firing zone: Magnesium iron spinel bricks (MgO≥85%) withstand 1450℃ continuous heat load;
Preheater cyclone: Anti-scaling silicon carbide bricks (SiC≥70%) reduce the frequency of crusting by 60%;
2. Glass Kiln
Melting furnace wall: Cast AZS-41# bricks (ZrO₂ 41%) have a 3-year/overhaul resistance to glass liquid corrosion;
Material channel system: α-β alumina bricks achieve ultra-low glass phase content (<1%);
Energy and environmental protection field
1. Waste incineration power generation
Grate incinerator: Chrome corundum mullite bricks (Cr₂O₃ 10%-15%) resists HCl (concentration ≤15%) corrosion;
Waste heat boiler: Cordierite refractory module (2MgO·2Al₂O₃·5SiO₂) for rapid maintenance;
2. Coal gasification unit
Gasifier radiation section: High-purity corundum bricks (Al₂O₃≥99%) withstand 6.5MPa operating pressure;
Synthesis gas channel: Silicon carbide wear-resistant lining (hardness ≥9 Mohs);
Breakthroughs in emerging application scenarios
1. New energy material preparation
Lithium battery positive electrode material kiln: High-purity alumina push plate (Al₂O₃≥99.5%) for pollution-free sintering;
Photovoltaic polysilicon ingot furnace: Isostatic pressing of silicon nitride ceramic components (thermal conductivity ≥25 W/m·K);
2. Aerospace field
Rocket engine test bench: Zirconia toughened alumina (ZTA) composite material can withstand 500 cycles of thermal shock;
Hypersonic wind tunnel: Fiber-reinforced silicon carbide ceramics achieve 3000℃/30 seconds transient thermal protection;